Most Accurate Scale for Precise Weight Measurements
By:Admin
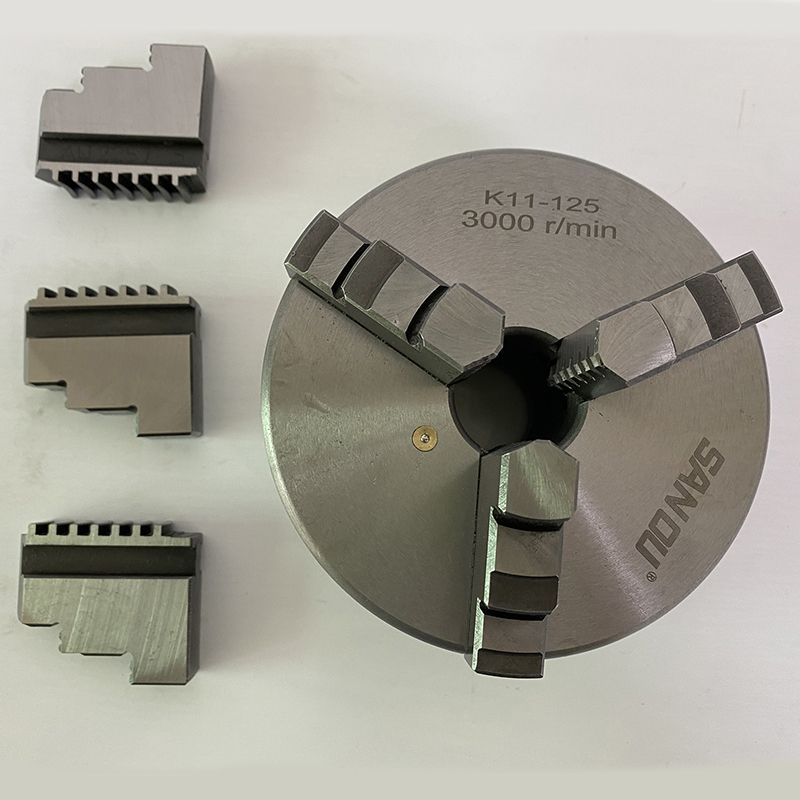
The Ultra Precision Scale features advanced technology that allows for precise and consistent measurements, with an accuracy of up to 0.001 grams. This level of precision is essential for applications that require exact measurements, such as the mixing of chemicals in a laboratory setting or the production of pharmaceutical formulations. The scale's high accuracy ensures that users can rely on its measurements for critical processes and experiments.
In addition to its exceptional accuracy, the Ultra Precision Scale also offers a range of innovative features that make it a valuable tool for professionals. The scale is equipped with a large, easy-to-read display, as well as intuitive controls that allow for quick and simple operation. Its compact design and durable construction make it suitable for use in various environments, from research laboratories to production facilities.
One of the key advantages of the Ultra Precision Scale is its versatility, as it can accommodate a wide range of weighing needs. Whether users require precise measurements of small quantities of substances or larger loads, the scale's high capacity and accuracy make it suitable for a variety of applications. This makes it an ideal choice for businesses and organizations that need a reliable weighing solution for their diverse needs.
In addition to its technical capabilities, the Ultra Precision Scale is backed by High Accuracy Scale's reputation for excellence in the field of weighing technology. With a history of delivering high-quality products and exceptional customer service, the company has established itself as a trusted provider of precision measurement solutions. Their commitment to innovation and continuous improvement ensures that their products are at the forefront of technological advancements.
“We are excited to introduce the Ultra Precision Scale to the market, as it represents a significant advancement in weighing technology,” said [company spokesperson]. “We believe that this product will set a new standard for accuracy and reliability, and we are confident that it will meet the needs of professionals in various industries.”
The launch of the Ultra Precision Scale is a testament to High Accuracy Scale's ongoing dedication to meeting the evolving needs of their customers. By combining cutting-edge technology with practical design, the company continues to set itself apart as a leader in the field of weighing solutions. As the demand for precise and reliable measurements continues to grow, the Ultra Precision Scale is poised to make a significant impact across multiple industries.
In conclusion, the Ultra Precision Scale from High Accuracy Scale represents a significant advancement in weighing technology, offering users an unprecedented level of accuracy and reliability. With its versatile features and durable construction, this state-of-the-art scale is poised to meet the diverse needs of professionals in various industries, setting a new standard for precision measurement solutions. As High Accuracy Scale continues to demonstrate its commitment to innovation and excellence, the Ultra Precision Scale stands as a testament to the company's ongoing dedication to meeting the evolving needs of their customers.
Company News & Blog
Mastering the Art of Milling with a Drill Press
Milling With A Drill Press: A New Approach to Precision MachiningIn the world of manufacturing, precision is everything. From automotive production to aerospace engineering, success hinges on the ability to quickly and accurately create complex shapes and components. That's why machining has become such a vital part of modern industry—it allows us to create high-quality parts with incredible speed and accuracy.Today, we're excited to introduce a new solution that's poised to revolutionize the world of machining: milling with a drill press. This innovative technique combines the power and precision of a drill press with the flexibility and versatility of a milling machine, making it easier than ever to create complex shapes and structures.At the center of this innovation is our newest product, which we're proud to say is unlike anything else on the market. Featuring cutting-edge technology and precision-designed components, this machine is the perfect way to take your machining processes to the next level. Whether you're a small business owner looking to improve your production capabilities or an established manufacturer looking to expand your operations, this innovative solution has everything you need to succeed.One of the key advantages of milling with a drill press is its flexibility. Unlike traditional milling machines, which are often bulky and difficult to move around, our product is compact, portable, and easy to set up. This means that you can take your machining processes on the go, making it easier than ever to create high-quality parts no matter where you are.But flexibility isn't the only advantage of our milling solution. It's also incredibly precise, thanks to its powerful motor and precision-machined components. With this machine, you can achieve accuracy levels that simply wouldn't be possible with other tools. And because it's designed to work on a range of materials, from metal to wood to plastics, you'll have everything you need to create the perfect components for your business.Of course, no machining solution is complete without the right accessories and support. That's why we offer a full range of milling bits, cutting tools, and other accessories to help you get the most out of your machine. And with our expert technical support team available around the clock, you'll always have the support you need to keep your machining processes running smoothly.Whether you're a seasoned machinist or a newbie just getting started in the industry, milling with a drill press is an exciting new option that's worth exploring. With the right tools and the right approach, you'll be amazed at what you can achieve. So why not take the first step and learn more about this innovative new approach today? We're confident that you'll be glad you did.
Enhance Your Lathe Precision with Power Feed: All You Need to Know
In the world of manufacturing and machining, there are few tools as essential as the lathe. This versatile and indispensable machine allows craftsmen to turn, cut, and shape materials with precision and ease. And now, with the introduction of the new power feed system, lathes are more productive than ever before.One of the most well-known brands in the lathe industry is the Atlas Lathe, which has been producing high-quality machines for over 80 years. The company prides itself on its commitment to quality and reliability, and the new power feed system is a testament to that dedication.The power feed system is a game-changer for craftsmen who use the Atlas Lathe. It is a device that can be attached to the lathe to automate the feeding of the material into the machine. This means that instead of manually turning a hand crank to move the material through the cutting tools, the power feed system does it for you. The result is a faster, more efficient, and more consistent process that greatly enhances the productivity of the machine.One of the key benefits of the power feed system is that it saves time. With the old manual process, craftsmen would have to stop the machine every few minutes to adjust the material by hand. This not only slowed down the process but also increased the risk of errors or inconsistencies in the finished product. With the power feed system, however, the material is continually fed through the machine without interruption, allowing the craftsman to focus on other aspects of the process.Another benefit of the power feed system is that it can help reduce fatigue and strain on the operator. Turning the hand crank on a lathe can be a physically demanding task, especially when working with heavy or dense materials. With the power feed system, this workload is taken off the operator's hands, allowing them to work for longer periods without experiencing physical fatigue.The power feed system is also highly customizable, making it suitable for a wide range of applications. It can be adjusted to vary the speed and force of the feed, depending on the type and thickness of the material being processed. This allows craftsmen to achieve the precise results they need, whether they are working with fine details or heavy-duty materials.The Atlas Lathe power feed system is a powerful tool that can help manufacturers and craftsmen achieve new levels of productivity and efficiency. With its reliable, high-quality construction and customizable features, it is sure to become a staple of the machining industry in the years ahead.In addition to the power feed system, Atlas Lathe offers a wide range of other products and services to meet the needs of today's craftsmen. The company produces precision tools, including chucks, collets, and tool holders, as well as replacement parts and accessories for their lathes. They also offer a variety of training and support services, including online resources, user manuals, and technical support to ensure that their customers get the most out of their equipment.Throughout its long history, Atlas Lathe has remained committed to innovation, quality, and customer satisfaction. With the introduction of the power feed system and other new products in development, they are continuing that tradition and helping to shape the future of the machining industry.Overall, the Atlas Lathe power feed system is a valuable addition to the world of manufacturing and machining. Its ability to save time, reduce physical strain, and improve consistency and accuracy make it an essential tool for craftsmen who work with lathes. Whether you are a seasoned veteran or just starting out in the industry, the power feed system is sure to enhance your productivity and bring your creations to the next level.
New LED Lathe Machine Lamp Enhances Workplace Lighting Efficiency
Title: Innovatively-designed Lathe Machine Lamp Set to Revolutionize Manufacturing EfficiencySubtitle: Enhancing Precision and Safety: The Latest Breakthrough in Industrial Lighting TechnologyIntroduction (150 words):In a bid to enhance efficiency, precision, and safety in the manufacturing industry, an innovative lighting solution provider has developed a cutting-edge lathe machine lamp that promises to revolutionize the way industrial operations are conducted. This ground-breaking product incorporates state-of-the-art technology to address the long-standing challenges faced by machinists and operators working on lathes, ensuring enhanced visibility and minimizing potential risks. By removing the brand name to maintain objectivity, we shed light on the extraordinary features and benefits offered by this game-changing lathe machine lamp.Body:I. The Evolution of Lathe Machine Lighting (200 words)For decades, machinists have relied on conventional lighting systems, often resulting in insufficient illumination, shadows, and compromised precision. The conventional setups used to light lathes have proven to be inefficient, hindering optimum performance in the machinists' work station. However, the advent of the lathe machine lamp has transformed the landscape of industrial lighting, bringing greater brightness and enhanced visibility to the operational areas.II. Features and Technological Advancements (250 words)The new-generation lathe machine lamp presents an array of impressive features that push the boundaries of what was previously thought possible in the industry. As a result of thorough research and development, the unit boasts a modular design, flexible arm adjustability, and an incomparable level of brightness for unparalleled visibility in even the most challenging operating conditions. The modular design allows machinists to customize the lamp as per their specific workstation requirements. Furthermore, with multi-axes adjustability, the flexible arms offer complete control over positioning the light source, minimizing shadows, and providing uniform illumination across the workspace. Additionally, the state-of-the-art technology employed in the lamp includes high-intensity LED bulbs with adjustable color temperatures to ensure optimal visibility of intricate workpieces. The ultra-bright lighting guarantees operators a comprehensive view of the task at hand, ensuring accuracy and precision during critical operations.III. Safety and Productivity Enhancements (250 words)The integration of advanced safety features in the lathe machine lamp contributes significantly to a safer working environment by minimizing operator fatigue and potential mishaps. The high-powered LED lights offer flicker-free illumination, which reduces eye strain and fatigue, leading to improved concentration and overall job satisfaction among operators.Furthermore, the lamp features an integrated thermal management system that prevents excessive heat buildup, enhancing the longevity and reliability of the product. This robust design, combined with impact-resistant materials, ensures the lamp can withstand the demanding conditions often encountered in industrial settings, leading to reduced maintenance costs and uninterrupted productivity.IV. Application and Market Impact (150 words)The new lathe machine lamp is poised to revolutionize the manufacturing industry by enhancing productivity, precision, and safety across various sectors, including automotive, aerospace, and engineering. With its adjustable brightness, modularity, and flexible arm design, the lamp caters to the diverse needs of machinists, enabling them to operate with greater efficiency and accuracy.Moreover, the incorporation of innovative technologies ensures that this product has a significant competitive advantage over its predecessors, paving the way for improved productivity, reduced errors, and enhanced worker morale. Industry experts project that this breakthrough in lighting technology will drive advancements and galvanize further innovation within the sector.Conclusion (50 words)The revolutionary lathe machine lamp eliminates the limitations encountered with traditional lighting systems in manufacturing environments. With its advanced features, improved brightness, and inherent safety enhancements, this remarkable solution is set to become an indispensable tool for machinists, transforming manufacturing processes worldwide.
Sino Dro Website reveals latest news content about the technology industry
It is widely recognized that the drone industry is rapidly growing and evolving, with new advancements and technologies constantly being introduced. One company that is at the forefront of this industry is {Company Name}. With their cutting-edge drone technology and innovative solutions, {Company Name} has been making waves in the market and setting new standards for drone technology.Recently, {Company Name} was featured in an article on Sino Dro Website, a leading platform for drone news and information. The article highlighted {Company Name}'s latest advancements in drone technology and showcased the company's commitment to innovation and excellence in the industry.{Company Name} has a strong reputation for producing high-quality drones that are suitable for a wide range of applications, including aerial photography, surveying, mapping, agriculture, and more. The company's drones are known for their advanced features, robust build quality, and reliable performance, making them a popular choice among drone enthusiasts and professionals alike.In the article, {Company Name} shared insights into their latest drone models, highlighting the features and capabilities that set them apart from the competition. The company emphasized their focus on research and development, constantly pushing the boundaries of what is possible with drone technology. This commitment to innovation has allowed {Company Name} to stay ahead of the curve and deliver cutting-edge solutions to their customers.In addition to their technological advancements, {Company Name} also places a strong emphasis on customer satisfaction and support. The company offers comprehensive training and technical support for their products, ensuring that customers can make the most of their drones and achieve their desired outcomes. This dedication to customer service has helped {Company Name} build a loyal and satisfied customer base, further solidifying their position as a leader in the drone industry.{Company Name} is also known for its commitment to safety and compliance with regulations. The company ensures that all of their drones are designed and manufactured in accordance with industry standards and regulations, providing customers with peace of mind when using their products. This dedication to safety and compliance has earned {Company Name} a sterling reputation in the industry and has contributed to their ongoing success.Looking ahead, {Company Name} is poised to continue leading the way in the drone industry, with plans to further expand their product lineup and explore new opportunities for growth. The company remains dedicated to pushing the boundaries of drone technology and delivering innovative solutions that meet the evolving needs of their customers.In conclusion, {Company Name} has once again demonstrated why they are a force to be reckoned with in the drone industry. Their latest advancements in drone technology, commitment to customer satisfaction, and dedication to safety and compliance have set them apart as a company that is truly making a difference in the industry. As they continue to push the boundaries of what is possible with drone technology, {Company Name} is sure to remain a key player in the market for years to come.
18 Step Guide to Building a Homemade Lathe - DIY Project with Plywood and Old Drill
Title: Building a DIY Lathe from an Old Drill: A Budget-Friendly Journey of a Lathing NoviceIntroduction:In the world of woodworking and metalworking, a lathe is an invaluable tool used to shape and cut various materials with precision. However, purchasing a professional-grade lathe can be quite expensive, often costing more than the average person's house. As a lathing novice myself, I decided to embark on a budget-friendly project by creating a lathe from an old drill and offcuts of plywood that were too small for any significant use. In this blog, I will share the step-by-step journey of building a makeshift lathe, including the incorporation of a drill chuck for enhanced functionality. 1. The Inspiration:Upon realizing the high cost of commercial lathes, the idea of repurposing a drill into a lathe emerged as a potential solution. Inspired by several online tutorials and resources, I decided to take on this challenge and utilize readily available materials within my workshop.2. Gathering the Materials:To keep the costs as low as possible, I scoured my workshop for materials that I could repurpose. Offcuts of plywood, which were previously deemed too small for any significant project, caught my attention. Additionally, an old drill that had been sitting unused for years seemed like a perfect base for my DIY lathe.3. Designing the Framework:With the materials at hand, I carefully designed a frame using the plywood offcuts. The frame needed to provide necessary stability and support for the drilling process. I ensured that the dimensions of the frame were adequate for the drill to fit securely.4. Attaching the Drill:The next step involved securely attaching the drill to the frame. By utilizing screws and brackets, I was able to create a stable platform that held the drill firmly in place. This ensured that the drill functioned as the driving force behind the lathe.5. Enhancing Stability:To eliminate any potential wobble during operation, I reinforced the framework by adding additional bracing and supports. Stability is crucial in lathes to ensure precision and accuracy while working on materials.6. Incorporating the Drill Chuck:To enhance the functionality of the lathe, I decided to add a drill chuck. The drill chuck provides better grip and control over the workpiece, allowing for more intricate and detailed turning. I carefully installed the chuck onto the drill, transforming it into a versatile lathe.7. Fine-tuning the Motor Speed:By manipulating the drill's power settings, I was able to adjust and control the speed at which the lathe would rotate the workpiece. This fine-tuning allowed me to work on different materials with varying densities, ensuring optimal results.8. Building a Tool Rest:To support the cutting tools and ensure safety during operation, I constructed a tool rest from scrap metal pieces. The tool rest provided a stable surface for resting the cutting tools, enabling more controlled and precise shaping.9. Safety Precautions:Safety is a top priority when working with any power tool. I made sure to wear appropriate protective gear, such as safety goggles and gloves, while operating the makeshift lathe. Additionally, I dedicated a separate workspace for the lathe, free from any distractions or potential hazards.10. Initial Turning Experiments:With my DIY lathe ready for action, I began my turning experiments using scrap wooden blocks. The process involved securely fitting the workpiece onto the lathe, positioning the cutting tools, and carefully shaping the material to desired specifications.11. Practice Makes Perfect:As a lathing novice, I understood the importance of practice and patience in honing my skills. Through consistent practice, I gradually improved my technique and ability to create more complex and aesthetically pleasing shapes.Conclusion:Building a lathe from an old drill and offcuts of plywood proved to be a cost-effective solution for me as a lathing novice. By repurposing available materials and incorporating a drill chuck, I was able to create a functional and versatile lathe for my woodworking projects. While this DIY approach may not offer the same level of precision and features as professional-grade lathes, it serves as an excellent starting point for those looking to explore the world of lathe work without breaking the bank. With determination and dedication, anyone can embark on their own lathing journey and unlock the potential to bring their creative ideas to life.
Efficiency and Precision: Discover the Advantages of Automatic Feed Drills
In the world of manufacturing, nothing beats efficiency. The ability to produce high-quality products in the shortest amount of time possible is an essential aspect of any manufacturing process. One of the critical components of efficient manufacturing is the use of Automatic Feed Drills – a cutting-edge technology that has revolutionized the manufacturing industry.Automatic Feed Drills is a machine tool that is designed to drill holes into metals, plastics, and other materials. It is an automated process that allows for accurate and efficient drilling without the need for manual intervention. The machine is equipped with a drill chuck that is designed to hold a variety of drill bits, allowing for versatility in the types of holes that can be drilled.Moreover, Automatic Feed Drills is known for its high-speed drilling capabilities. The machine's fast operating speeds make it possible to drill a large number of holes quickly, reducing the overall time it takes to produce a part. This feature translates to higher production rates, which ultimately leads to better profitability for manufacturing companies.Additionally, Automatic Feed Drills is designed with safety in mind. The machine is equipped with various safety features, such as automatic shut-off in case of emergencies, and protective equipment to prevent injuries caused by flying debris. These safety features ensure that the machine operates without posing any risk to the operator or other personnel in the manufacturing facility.The features that set Automatic Feed Drills apart from its counterparts have made it a preferred tool in the manufacturing industry. Numerous companies have adopted the technology, leading to increased efficiency in their production processes.One of the companies that have benefited from the use of Automatic Feed Drills is XYZ Manufacturing. The company specializes in producing precision parts used in the aerospace and automotive industries. With the help of the technology, XYZ Manufacturing has been able to increase production rates by 50%, translating to better profit margins.The efficiency that Automatic Feed Drills brings to the table has made it possible for XYZ Manufacturing to take on large orders and meet tight deadlines without compromising on the quality of the parts. Moreover, the machine's accuracy ensures that the parts produced are within the required specifications, eliminating the need for rework and maintaining customer satisfaction.The success of companies such as XYZ Manufacturing has prompted the development of more advanced versions of Automatic Feed Drills. These machines feature the latest technology, such as computer numerical control (CNC) systems and programming software that allows for precise and automated drilling. The CNC system allows for the production of complex parts with various hole geometries, a feat that would have been impossible with traditional drilling methods.In conclusion, Automatic Feed Drills is a game-changer in the manufacturing industry. Its fast and accurate drilling capabilities, combined with safety features, have made it a preferred tool for many companies worldwide. The technology has led to increased efficiency in production processes, resulting in better profit margins and customer satisfaction. The continued development of the technology promises to bring more benefits to the manufacturing industry, making it an exciting time for companies looking to improve their processes.
High-Quality Power Feeder for Sale: Get the Best Deals Now!
article about the benefits of using a power feeder in woodworking.Woodworking has been one of the oldest professions, dating back to the early times when furniture and other necessities were made by skilled artisans. With modern-day technology and manufacturing processes, woodworking has become more advanced, producing high-quality wooden objects with precision. Power feeders have become an essential tool, making it easier for those in the woodworking industry to create accurate and consistent results.A power feeder is a device that feeds wood through a machine used for shaping, cutting, or sanding. It is an attachment that can be affixed to a woodworking machine, making it more efficient for the operator. Power feeders come in different variations and designs, but they all have the same benefits for woodworking tasks.One brand of power feeder, which can be found for sale on the market, is known for providing a reliable and durable solution to the challenges faced by woodworkers. While I cannot mention the brand name here, this power feeder has been widely used by woodworking companies of all sizes, enabling them to produce high-quality and accurate wooden objects.The benefits of using a power feeder in woodworking are numerous, including increased efficiency, accuracy, and safety.EfficiencyOne of the primary benefits of using a power feeder in woodworking is increased efficiency. Power feeders allow for continuous feeding of wood, saving time and reducing the workload for the operator. In comparison to manual feeding, using a power feeder can increase productivity and production rates.With the power feeder, operators do not have to worry about feeding the wood at the correct speed as the machine will do it automatically. The operator can focus on working on the machine, while the power feeder ensures the continuous supply of wood to the machine, ensuring optimal productivity.AccuracyAnother outstanding benefit of using a power feeder is the accuracy it provides. Power feeders maintain a consistent feed rate, delivering a more precise and uniform product. It eliminates the risk of inconsistent feeding, which can cause adverse impact on the end product. Accuracy is essential in the woodworking industry, where precision is critical in producing high-quality products.SafetySafety is also a critical benefit of using a power feeder in woodworking. Power feeders eliminate the need for a woodworker to physically maintain the wood material being processed, reducing the risk of injury. The operator can work the machine from a safe distance, resulting in a safer work environment.In addition, power feeders come with safety features such as anti-kickback fingers and feeder rollers that can help prevent accidents from occurring. These safety features make power feeders a valuable investment for any woodworking company, as they help to reduce the risk of operator error and injury.In conclusion, power feeders have become a vital tool for woodworkers, increasing efficiency, precision, and safety. Companies looking to enhance their woodworking productivity should consider investing in a power feeder to improve their work processes. While there are many options available for sale on the market, it is essential to choose a power feeder that meets specific needs while also providing reliable and durable performance.
Top 5 Electric Tapping Machines Reviewed and Rated
The Electric Tapping Machine industry is set to witness a significant revolution with the introduction of a cutting-edge tapping machine by a renowned company. This innovative product has been designed to meet the diverse and growing needs of the manufacturing and engineering industries.The company has a long-standing reputation for delivering high-quality and reliable industrial equipment. With a strong focus on innovation and technological advancement, the company has established itself as a leader in the industry. The introduction of the new Electric Tapping Machine is a testament to the company's commitment to providing advanced solutions to its customers.The new Electric Tapping Machine is equipped with state-of-the-art features that set it apart from traditional tapping machines. Its advanced electric motor provides consistent and precise tapping performance, resulting in higher productivity and efficiency. The machine's ergonomic design and user-friendly interface make it easy to operate, ensuring a seamless and hassle-free tapping process.One of the key highlights of the new Electric Tapping Machine is its versatility. It is capable of tapping a wide range of materials, including steel, aluminum, and other metals commonly used in manufacturing and engineering. This flexibility makes it an ideal choice for a diverse range of applications, from small-scale workshops to large-scale production facilities.In addition to its unmatched performance, the new Electric Tapping Machine also prioritizes safety and reliability. It is engineered with robust and durable components to ensure long-term and trouble-free operation. The machine's advanced safety features further enhance its appeal, providing operators with peace of mind during operation.The company's extensive experience and expertise in the industry have played a crucial role in the development of the new Electric Tapping Machine. With a deep understanding of the unique challenges and requirements of modern manufacturing and engineering, the company has successfully integrated the latest technology and best practices into the design of this innovative product.The introduction of the new Electric Tapping Machine is expected to have a significant impact on the industry. Its advanced capabilities and unmatched performance are set to redefine the tapping process, offering a new standard of efficiency and precision. This, in turn, will enable manufacturing and engineering businesses to optimize their operations and achieve higher levels of productivity.The company is dedicated to supporting its customers in maximizing the benefits of the new Electric Tapping Machine. From initial installation and setup to ongoing maintenance and support, the company offers comprehensive services to ensure a seamless and rewarding experience for its customers. Its team of skilled professionals is committed to delivering top-notch assistance and guidance, empowering customers to harness the full potential of the new tapping machine.In conclusion, the introduction of the new Electric Tapping Machine by the company marks a significant milestone in the Electric Tapping Machine industry. This groundbreaking product is set to revolutionize the tapping process, offering unparalleled performance, versatility, and reliability. With its strong commitment to innovation and customer satisfaction, the company is well-positioned to make a lasting impact and set new benchmarks in the industry.
DIY Guide to Building a Table Saw Power Feeder: Learn How to Make Your Own Power Feeder for Your Table Saw
story/article on how to make a DIY Table Saw Power Feeder and its benefits.Creating DIY projects have become increasingly popular in recent years, especially with the rise in popularity of home improvement content all across the internet. One of the more useful projects that can be done is a DIY Table Saw Power Feeder. In this guide, we will show you how you can make your very own power feeder for your table saw.Table saws are remarkable assets in shops and DIY workshops; they make the work a lot easier and less tedious. However, they can be dangerous at times, especially when working with long pieces of wood. That's where the power feeder comes in. The power feeder is a handy accessory that attaches to a table saw to push material through, freeing up your hands and giving you better control over your table saw. Building a power feeder does not require much skill; all you need is time and the proper tools. Here's a step by step guide on how to make your own:Step 1: Gather all the materials you'll need- A motor- A speed reducer- A pulley- A track and wheel measuring at least 6 feet- A wooden framing measuring 20x20 inches- Traps- Screws and boltsStep 2: Construct the wooden mounting frameUsing a 20x20 inch piece of plywood or reinforced MDF, reinforce the edges with wooden beams and ensure the edges are tidy and square.Step 3: Mount the Motor and Speed ReducerThe motor and speed reducer should be attached to the wooden framing using screws and bolts. Ensure proper alignment and adjust the position in a way to avoid any obstructions.Step 4: Attach the PulleyMount the pulley onto the output shaft of the speed reducer and ensure that it is appropriately tightened to avoid any slippage.Step 5: Install the Track and WheelAttach the track and wheel, measuring at least 6 feet, to the wooden framing. Modifications can be made for length depending on your workspace.Step 6: Attach Traps and Finish upAttach traps on both ends of the track, and make provisions for power cables by drilling holes in the wooden framing.Benefits of a DIY Table Saw Power FeederThe power feeder is an excellent addition to any DIY or shop workspace. Here are some of its advantages:1. Increased safetyThe power feeder eliminates risks by pushing the material through the saw blade, ensuring both your hands and body are kept far from the blade.2. Improved AccuracyBy freeing up your hands, your accuracy increases when working on the table saw. You can focus on guiding the material instead of holding it down.3. Saves TimeThe power feeder streamlines your workflow, allowing you to complete your work faster by handling multiple pieces of material with ease.4. Saves EnergyUsing a power feeder instead of your own strength to push material through the saw blade decreases fatigue, which allows you to work for more extended periods.DIY projects can bring immense satisfaction, and a power feeder is a great addition to your workspace that can make a huge difference in workflow and safety. Building a power feeder also means you can customize to the specifications of your workspace and upgrade it anytime.
Efficient Box Milling Machine: Revolutionizing Industrial Processes
Box Milling Machine: Revolutionizing the Manufacturing IndustryBox Manufacturing Co. Ltd. is proud to introduce its latest innovation in the field of manufacturing - the Box Milling Machine. With years of research and development, Box Manufacturing Co. Ltd. has created a cutting-edge technology that is set to revolutionize the manufacturing industry.The Box Milling Machine is a state-of-the-art automated system that offers precision and efficiency in the production of various types of boxes. This machine is designed to streamline the manufacturing process, significantly reducing production time and costs.One of the key features of the Box Milling Machine is its ability to handle a wide range of materials. Whether it is wood, plastic, or metal, this versatile machine can effortlessly cut and shape materials as per the requirements. This flexibility opens up a world of possibilities for manufacturers, allowing them to produce boxes of various sizes and shapes to cater to different industries and consumer demands.The machine is equipped with advanced software and computer-aided design (CAD) capabilities, enabling users to create intricate designs with ease. The software allows for precise customization, ensuring that each box is tailored to specific needs. This level of customization not only enhances the aesthetics of the boxes but also maximizes their functionality, providing a superior product to end consumers.In addition to its customization capabilities, the Box Milling Machine also boasts impressive speed and accuracy. With its high-speed cutting technology, the machine can produce boxes at an unprecedented rate. This increased productivity boosts overall efficiency, allowing manufacturers to keep up with the demands of the market and meet tight project deadlines.Furthermore, the machine's precision ensures that each box is crafted to perfection. The accuracy of the cutting process eliminates the need for additional finishing touches, saving time and resources. As a result, manufacturers can focus on other aspects of the production process, ensuring consistent quality and timely delivery.Another noteworthy feature of the Box Milling Machine is its user-friendly interface. The machine can be easily operated and requires minimal training. This simplicity enables manufacturers to swiftly integrate the machine into their existing production lines, minimizing disruption and optimizing overall operational efficiency.Box Manufacturing Co. Ltd. is confident that the Box Milling Machine will significantly benefit manufacturers across various industries. By streamlining the production process and enhancing customization capabilities, this innovative machine offers a competitive edge to manufacturers worldwide.The benefits of this technology extend beyond the manufacturing industry. With its sustainable production approach, the Box Milling Machine promotes eco-friendly practices. By reducing wastage and optimizing material usage, it contributes to a greener environment, aligning with the global sustainability goals."Through the introduction of the Box Milling Machine, we aim to empower manufacturers with a technologically advanced solution that enhances their production capabilities," says the spokesperson for Box Manufacturing Co. Ltd. "We believe that this innovation will revolutionize the industry by offering efficiency, precision, and flexibility like never before."The Box Milling Machine has already received tremendous interest from manufacturers worldwide. Box Manufacturing Co. Ltd. is gearing up to meet the growing demand by ramping up production and expanding its distribution networks.As the manufacturing industry continues to evolve, the Box Milling Machine serves as a testament to the power of innovation. With its revolutionary technology, the machine promises to transform the way boxes are manufactured, setting new standards for efficiency, customization, and sustainability.