Create Your Own DIY Lathe Accessories for Better Woodworking Results
By:Admin
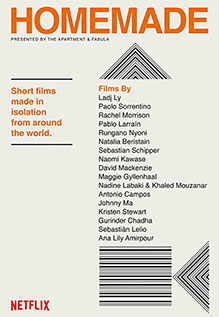
Why Homemade Lathe Accessories?
While there are certainly plenty of lathe accessories handles on the market, many of them can be expensive or may not fit your specific needs. That's where making your own homemade lathe accessories comes in. Not only can you save money, but you can also customize your accessories to fit your exact specifications and preferences.
Some of the most popular types of homemade lathe accessories include:
· Chucks and faceplates
· Tool rests
· Drive centers and live centers
· Collets and mandrels
· And more...
One of the most important considerations when choosing a lathe accessory is the handle. Whether you're turning a bowl or a spindle, having a comfortable, sturdy handle on your accessory can make a big difference in the quality of your work.
Homemade Lathe Accessories Handles
Fortunately, making your own lathe accessory handle is a relatively easy process. Here are a few tips to get you started:
1. Choose your material: There are a variety of materials you can use for your lathe accessory handle, including wood, metal, and plastic. Consider the weight, durability, and feel of each material before making your choice.
2. Measure: Take precise measurements of the existing handle you want to replace or of the accessory itself. Make note of the diameter, length, and any other specifications that are important to the design of your handle.
3. Design your handle: Sketch out your design on paper or use a 3D modeling software to create a digital model. Make sure the handle is comfortable to hold and easy to grip. Consider adding texturing or other features to improve your grip.
4. Cut and shape your material: Once you have your design, it's time to cut and shape your material. Depending on the material you choose, you may need different tools such as a lathe, drill press, or band saw. Follow your design closely, taking care to create a smooth, even finish.
5. Install your new handle: Once your handle is complete, it's time to install it on your lathe accessory. Make sure it is securely attached and that it fits snugly against the accessory. Test your handle to ensure it is comfortable to use and functional.
Conclusion
Making your own homemade lathe accessories can be a great way to save money and customize your tools to fit your specific needs. Whether you're making a new chuck or simply replacing a handle, taking the time to create a comfortable, sturdy accessory can help improve the quality of your work. So why not give it a try? With a little bit of creativity and some basic tools, you can create your own lathe accessory handles that will stand up to years of use.
Company News & Blog
Create Your Own DIY Lathe Accessories for Better Woodworking Results
When it comes to metalworking and woodworking, having the right tools can make all the difference in the world. And even if you have a great lathe, there may be times when you need a specific accessory to make your project work. That's where homemade lathe accessories come in. In this blog post, we'll talk about the importance of having the right accessories for your lathe and explore some of the best homemade options for lathe accessories handles.Why Homemade Lathe Accessories?While there are certainly plenty of lathe accessories handles on the market, many of them can be expensive or may not fit your specific needs. That's where making your own homemade lathe accessories comes in. Not only can you save money, but you can also customize your accessories to fit your exact specifications and preferences.Some of the most popular types of homemade lathe accessories include:· Chucks and faceplates· Tool rests· Drive centers and live centers· Collets and mandrels· And more...One of the most important considerations when choosing a lathe accessory is the handle. Whether you're turning a bowl or a spindle, having a comfortable, sturdy handle on your accessory can make a big difference in the quality of your work.Homemade Lathe Accessories HandlesFortunately, making your own lathe accessory handle is a relatively easy process. Here are a few tips to get you started:1. Choose your material: There are a variety of materials you can use for your lathe accessory handle, including wood, metal, and plastic. Consider the weight, durability, and feel of each material before making your choice.2. Measure: Take precise measurements of the existing handle you want to replace or of the accessory itself. Make note of the diameter, length, and any other specifications that are important to the design of your handle.3. Design your handle: Sketch out your design on paper or use a 3D modeling software to create a digital model. Make sure the handle is comfortable to hold and easy to grip. Consider adding texturing or other features to improve your grip.4. Cut and shape your material: Once you have your design, it's time to cut and shape your material. Depending on the material you choose, you may need different tools such as a lathe, drill press, or band saw. Follow your design closely, taking care to create a smooth, even finish.5. Install your new handle: Once your handle is complete, it's time to install it on your lathe accessory. Make sure it is securely attached and that it fits snugly against the accessory. Test your handle to ensure it is comfortable to use and functional.ConclusionMaking your own homemade lathe accessories can be a great way to save money and customize your tools to fit your specific needs. Whether you're making a new chuck or simply replacing a handle, taking the time to create a comfortable, sturdy accessory can help improve the quality of your work. So why not give it a try? With a little bit of creativity and some basic tools, you can create your own lathe accessory handles that will stand up to years of use.
Upgrade Your Milling Experience: 3 Axis Digital Readout Kit With Magnetic Encoders
, DRO Kit, Bridgeport Mill, CNC Machined Brackets, Step by Step Installation Guide, Custom-designed, Machine-dro.co.uk.If you're looking to improve the accuracy and precision of your Bridgeport turret milling machine, then you should definitely consider investing in a Magnetic Digital Readout (DRO) kit. The M-DRO 3 Axis Bridgeport 42 Table Mill DRO Kit, available at machine-dro.co.uk, is the perfect solution for you.This custom-designed kit comes with CNC machined brackets and a step-by-step, full-color installation guide to assist you with the installation process. It is specifically designed to fit onto the original Bridgeport turret milling machine, ensuring that it operates seamlessly and effectively.The Magnetic Digital Readout kit offers you a lot of advantages. First and foremost, it helps you to take accurate measurements easily and quickly. The digital readout display shows you the precise position of your tool and workpiece, eliminating the need for guesswork. This also saves you a significant amount of time and effort.Secondly, the Magnetic Digital Readout is highly versatile, allowing you to switch between different types of measurements quickly and easily. You can switch between inches and millimeters, as well as relative and absolute zero positions. With this kind of flexibility, you can tailor your measurements to suit your specific project requirements.Thirdly, the Magnetic Digital Readout is highly durable and resistant to wear and tear. It uses magnetic encoders that provide high-resolution measurements, ensuring that your readings are always accurate and dependable. It is a cost-effective way to extend the life of your milling machine and minimize maintenance expenses.Finally, the Magnetic Digital Readout kit is straightforward to install and use. The full-color installation guide offers detailed instructions, making it easy even for beginners to install the kit. Once installed, you can use it with ease, and the intuitive interface ensures that you can take measurements without any difficulty.In conclusion, the M-DRO 3 Axis Bridgeport 42 Table Mill DRO Kit is undoubtedly the best Magnetic Digital Readout kit in the market. It is custom-designed, highly versatile, durable, and easy to install and use. Get yours today from machine-dro.co.uk and experience the numerous advantages the kit offers.
Milling Machine Hold Down Clamp: Keep Your Workpiece Secure with T Slot Clamping Kit
article that highlights the importance of using a T slot clamping kit in milling machines and drill presses.In the world of mechanical engineering and fabrication, the use of milling machines and drill presses is quite common. These machines provide precise and accurate cuts and holes in different materials such as metals, plastics, and wood. However, the efficiency of these machines depends on the reliability of the hold-down kits used for securing the workpiece in place.A hold-down kit is an assembly of clamps, bolts, and nuts that are used to secure the workpiece to the milling machine table or drill press base. Without proper hold-down, the workpiece may move during the cutting process, resulting in inaccurate cuts or even damaging the machine or tool. Therefore, investing in a reliable and sturdy hold-down kit is crucial for ensuring the quality of the end product and the smooth operation of the machine.One of the most popular types of hold-down kits is the T slot clamping kit. It is named so because of the T-shaped groove present on the milling machine table or drill press base used for holding the clamps and bolts of the kit. The T slot clamping kit comprises several components such as T nuts, studs, step blocks, flange nuts, and clamps that are designed to fit perfectly in the T slot.The T slot clamping kit provides many advantages over other types of hold-down kits. Firstly, it is easy to install and remove, allowing for quick and efficient workpiece changes. Secondly, it provides a firm and secure hold on the workpiece, preventing any movement during the cutting process and ensuring accuracy in the end product. Finally, the T slot clamping kit is highly versatile, allowing it to be used in a variety of applications, including milling machines, drill presses, and even some CNC machines.One of the most trusted and reliable suppliers of T slot clamping kits in the market is Busy Bee Tools. With over 50 years of experience in the industry, Busy Bee Tools is a leading supplier of woodworking and metalworking tools, machinery, and accessories. The company offers a wide range of T slot clamping kits, including various sizes and configurations to suit specific machine requirements. Moreover, the kits are made of high-quality materials such as cast iron and steel, ensuring they can withstand high pressures and wear and tear.In conclusion, the importance of using a reliable hold-down kit, such as the T slot clamping kit, cannot be overstated. Investing in a high-quality kit from a trusted supplier like Busy Bee Tools will not only help improve the quality of the end product but also extend the lifespan of the machine itself. Therefore, it is crucial to prioritize the selection of a suitable hold-down kit when operating a milling machine or drill press to ensure safety, efficiency, and precision in the fabrication process.
18 Step Guide to Building a Homemade Lathe - DIY Project with Plywood and Old Drill
Title: Building a DIY Lathe from an Old Drill: A Budget-Friendly Journey of a Lathing NoviceIntroduction:In the world of woodworking and metalworking, a lathe is an invaluable tool used to shape and cut various materials with precision. However, purchasing a professional-grade lathe can be quite expensive, often costing more than the average person's house. As a lathing novice myself, I decided to embark on a budget-friendly project by creating a lathe from an old drill and offcuts of plywood that were too small for any significant use. In this blog, I will share the step-by-step journey of building a makeshift lathe, including the incorporation of a drill chuck for enhanced functionality. 1. The Inspiration:Upon realizing the high cost of commercial lathes, the idea of repurposing a drill into a lathe emerged as a potential solution. Inspired by several online tutorials and resources, I decided to take on this challenge and utilize readily available materials within my workshop.2. Gathering the Materials:To keep the costs as low as possible, I scoured my workshop for materials that I could repurpose. Offcuts of plywood, which were previously deemed too small for any significant project, caught my attention. Additionally, an old drill that had been sitting unused for years seemed like a perfect base for my DIY lathe.3. Designing the Framework:With the materials at hand, I carefully designed a frame using the plywood offcuts. The frame needed to provide necessary stability and support for the drilling process. I ensured that the dimensions of the frame were adequate for the drill to fit securely.4. Attaching the Drill:The next step involved securely attaching the drill to the frame. By utilizing screws and brackets, I was able to create a stable platform that held the drill firmly in place. This ensured that the drill functioned as the driving force behind the lathe.5. Enhancing Stability:To eliminate any potential wobble during operation, I reinforced the framework by adding additional bracing and supports. Stability is crucial in lathes to ensure precision and accuracy while working on materials.6. Incorporating the Drill Chuck:To enhance the functionality of the lathe, I decided to add a drill chuck. The drill chuck provides better grip and control over the workpiece, allowing for more intricate and detailed turning. I carefully installed the chuck onto the drill, transforming it into a versatile lathe.7. Fine-tuning the Motor Speed:By manipulating the drill's power settings, I was able to adjust and control the speed at which the lathe would rotate the workpiece. This fine-tuning allowed me to work on different materials with varying densities, ensuring optimal results.8. Building a Tool Rest:To support the cutting tools and ensure safety during operation, I constructed a tool rest from scrap metal pieces. The tool rest provided a stable surface for resting the cutting tools, enabling more controlled and precise shaping.9. Safety Precautions:Safety is a top priority when working with any power tool. I made sure to wear appropriate protective gear, such as safety goggles and gloves, while operating the makeshift lathe. Additionally, I dedicated a separate workspace for the lathe, free from any distractions or potential hazards.10. Initial Turning Experiments:With my DIY lathe ready for action, I began my turning experiments using scrap wooden blocks. The process involved securely fitting the workpiece onto the lathe, positioning the cutting tools, and carefully shaping the material to desired specifications.11. Practice Makes Perfect:As a lathing novice, I understood the importance of practice and patience in honing my skills. Through consistent practice, I gradually improved my technique and ability to create more complex and aesthetically pleasing shapes.Conclusion:Building a lathe from an old drill and offcuts of plywood proved to be a cost-effective solution for me as a lathing novice. By repurposing available materials and incorporating a drill chuck, I was able to create a functional and versatile lathe for my woodworking projects. While this DIY approach may not offer the same level of precision and features as professional-grade lathes, it serves as an excellent starting point for those looking to explore the world of lathe work without breaking the bank. With determination and dedication, anyone can embark on their own lathing journey and unlock the potential to bring their creative ideas to life.
Repairing an Old Power Feed Circuit Board for a Bridgeport Mill
As a machinist, my friend has always relied on his trusty Bridgeport mill to help him with his work. The milling machine has been his go-to tool for years and has helped him produce some of the highest quality workpieces. However, with age, the machine required some maintenance and upkeep. That's when the Servo Type 100 power feed came into play.The Servo Type 100 power feed is an old system that has been around for decades, and my friend had been using it for a long time. However, over time, the power feed circuit board began to malfunction, causing issues with the milling machine's performance. It was clear that the circuit board needed to be repaired, and my friend was determined to do it himself.Repairing a Servo Type 100 power feed circuit board is a complex process that requires a lot of technical expertise. My friend was determined to do it himself, and he got to work immediately. The first step was to remove the circuit board from the power feed unit and examine it closely for any visible damage or faults.Upon close inspection, he realized that the circuit board had suffered some damage due to exposure to moisture and other environmental factors. The damage was extensive, and it was evident that the board needed to be repaired or replaced entirely. Since the cost of replacing the circuit board was too high, my friend decided to repair it himself.To start with, he identified the faulty parts that were causing the issue and set about repairing them. He used a soldering iron, a multimeter, and other essential tools to replace and repair the faulty components. The process was time-consuming, and it required a lot of patience and attention to detail.After a few days of hard work, my friend managed to repair the circuit board successfully. He then reinstalled it back into the power feed unit and tested the system. The Servo Type 100 power feed was up and running again, functioning smoothly, and providing the required output to the milling machine.In conclusion, repairing a Servo Type 100 power feed circuit board is not an easy task, and it requires professional expertise. However, with the right tools, knowledge, and skills, anyone can repair a faulty circuit board and save a lot of money. As for my friend, he couldn't be happier with the repairs he made and is back to using his Bridgeport mill with his old Servo Type 100 power feed. However, with the advancements in technology, it's time to upgrade to the new Type 150 Servo Feed.
Revolutionary device creates a stir in the coffee world" becomes "Innovative Machine Disrupts the Coffee Industry
Introducing the Cutting-edge Home Lighting Solution In today's fast-paced world, technology is constantly evolving and transforming the way we live. One area that has seen significant advancements is home lighting. Gone are the days of traditional incandescent bulbs; now, homeowners are turning to energy-efficient and smart lighting solutions to enhance their living spaces. Among the latest innovations, the brand-new home lighting system, developed by a leading technology company, is set to revolutionize the way we illuminate our homes.The innovative home lighting machine, let's call it the "Grind Lamp," provides users with an unparalleled lighting experience. Boasting cutting-edge features and a sleek design, this smart lighting solution combines the efficiency of LED bulbs with advanced automation and customization options, making it the ideal choice for modern homeowners.One of the key features that sets the Grind Lamp apart from other lighting systems is its energy-efficient LED bulbs. LED technology consumes significantly less energy than traditional incandescent bulbs, allowing users to save on their electricity bills while reducing their carbon footprint. With the Grind Lamp, homeowners can enjoy exceptional lighting quality without compromising on sustainability.Additionally, the Grind Lamp incorporates smart automation features, making it a truly intelligent lighting solution. Utilizing advanced sensors and connectivity options, this system can adjust its brightness and color temperature according to the time of day, creating the perfect ambiance for any occasion. Whether you need bright, white light for a productive work session or warm, dimmed lighting for a cozy movie night, the Grind Lamp has got you covered.Furthermore, the Grind Lamp is equipped with an intuitive mobile app that puts the power of control in the hands of the user. Through the app, homeowners can easily manage and customize their lighting preferences, create personalized lighting schedules, and even synchronize their lights with music or other smart home devices. The app's user-friendly interface ensures a seamless user experience, allowing individuals to effortlessly tailor their lighting settings to suit their needs and moods.In addition to its exceptional functionality, the Grind Lamp also stands out for its sleek and modern design. With its minimalist yet elegant aesthetics, this home lighting solution seamlessly blends into any interior decor, adding a touch of sophistication to the living space. The lamp's sleek and slender frame, available in a variety of finishes, complements diverse design styles, from contemporary to traditional, making it a versatile choice for homeowners with different tastes.Moreover, safety is at the core of the Grind Lamp's design. The lamp is constructed with premium materials and undergoes rigorous testing to ensure its durability and reliability. With its robust build and adherence to international safety standards, homeowners can rest assured that the Grind Lamp will provide them with a long-lasting lighting solution that will beautifully illuminate their homes for years to come.With its energy-efficient LED bulbs, smart automation features, intuitive mobile app, and sleek design, the Grind Lamp revolutionizes home lighting. This innovative product offers homeowners an unparalleled lighting experience, allowing them to effortlessly customize and control their lighting preferences. Whether it's for aesthetic enhancement, energy savings, or convenience, the Grind Lamp is the ultimate lighting solution for today's smart homes.As the demand for smarter and more eco-friendly lighting options continues to grow, the Grind Lamp's arrival on the market is expected to make a significant impact. This cutting-edge home lighting solution is poised to transform the way we illuminate our living spaces, effortlessly combining technology, efficiency, and style. So, say goodbye to outdated lighting methods and embrace the future of home lighting with the Grind Lamp.
How to Replace and Adapt a Digital Scale for a DRO System
DRO PROS is a well-known brand in the digital readout (DRO) industry, offering high-quality scales and accessories to enhance machining accuracy and productivity. However, even the best equipment can fail sometimes, and that's what happened to my DRO PROS scale recently. It stopped counting at a certain point, which made me suspect that it had got contaminated with debris or dirt. So, I decided to investigate the issue and find a solution to fix it.After careful inspection and cleaning of the scale, I realized that the problem was not related to contamination, but rather to the scale itself. It appeared that one of the internal components had malfunctioned, which caused the scale to stop measuring accurately. I tried to fix it, but it was beyond repair, so I had to replace it with a new one.Since I was satisfied with the performance of my previous DRO PROS scale, I decided to order another one. However, this time I wanted to try something new, so I chose to adapt it with a Sino scale. Sino is a reputable brand in the DRO market, known for its reliable and precise scales that offer excellent value for money. By combining the DRO PROS display with a Sino scale, I hoped to get the best of both worlds – the quality of DRO PROS and the affordability of Sino.The process of adapting the Sino scale to the DRO PROS display was relatively simple. I purchased a SDS3MS Sino scale that matched the size and resolution of my previous DRO PROS scale. I also bought an adapter cable that allowed me to connect the Sino scale to the DRO PROS display. Once I received the items, I carefully removed the old scale and installed the new one. I connected the adapter cable and powered up the DRO PROS display. To my relief, the display showed the correct readings, and the scale worked perfectly fine.Now that I have been using the DRO PROS display and Sino scale for a while, I can say that I am happy with my choice. The accuracy and stability of the scale are excellent, which helps me achieve consistent and precise machining results. The DRO PROS display is also user-friendly and easy to navigate, with intuitive buttons and menus that allow me to customize the settings to my liking. Moreover, the price of the Sino scale was much lower than that of the DRO PROS scale, which helped me save some money without compromising on quality.In conclusion, adapting a Sino scale to a DRO PROS display is a viable option for those who want to upgrade their equipment without breaking the bank. Sino scales offer great value for money, while DRO PROS displays provide top-notch quality and performance. By combining the two, you can get a reliable and accurate digital readout system that enhances your machining capabilities. So, if you're in the market for a new DRO system, consider the DRO PROS display and Sino scale combo – you won't be disappointed!Keyword: Sino DRO SDS3MS
DIY Guide to Building a Table Saw Power Feeder: Learn How to Make Your Own Power Feeder for Your Table Saw
story/article on how to make a DIY Table Saw Power Feeder and its benefits.Creating DIY projects have become increasingly popular in recent years, especially with the rise in popularity of home improvement content all across the internet. One of the more useful projects that can be done is a DIY Table Saw Power Feeder. In this guide, we will show you how you can make your very own power feeder for your table saw.Table saws are remarkable assets in shops and DIY workshops; they make the work a lot easier and less tedious. However, they can be dangerous at times, especially when working with long pieces of wood. That's where the power feeder comes in. The power feeder is a handy accessory that attaches to a table saw to push material through, freeing up your hands and giving you better control over your table saw. Building a power feeder does not require much skill; all you need is time and the proper tools. Here's a step by step guide on how to make your own:Step 1: Gather all the materials you'll need- A motor- A speed reducer- A pulley- A track and wheel measuring at least 6 feet- A wooden framing measuring 20x20 inches- Traps- Screws and boltsStep 2: Construct the wooden mounting frameUsing a 20x20 inch piece of plywood or reinforced MDF, reinforce the edges with wooden beams and ensure the edges are tidy and square.Step 3: Mount the Motor and Speed ReducerThe motor and speed reducer should be attached to the wooden framing using screws and bolts. Ensure proper alignment and adjust the position in a way to avoid any obstructions.Step 4: Attach the PulleyMount the pulley onto the output shaft of the speed reducer and ensure that it is appropriately tightened to avoid any slippage.Step 5: Install the Track and WheelAttach the track and wheel, measuring at least 6 feet, to the wooden framing. Modifications can be made for length depending on your workspace.Step 6: Attach Traps and Finish upAttach traps on both ends of the track, and make provisions for power cables by drilling holes in the wooden framing.Benefits of a DIY Table Saw Power FeederThe power feeder is an excellent addition to any DIY or shop workspace. Here are some of its advantages:1. Increased safetyThe power feeder eliminates risks by pushing the material through the saw blade, ensuring both your hands and body are kept far from the blade.2. Improved AccuracyBy freeing up your hands, your accuracy increases when working on the table saw. You can focus on guiding the material instead of holding it down.3. Saves TimeThe power feeder streamlines your workflow, allowing you to complete your work faster by handling multiple pieces of material with ease.4. Saves EnergyUsing a power feeder instead of your own strength to push material through the saw blade decreases fatigue, which allows you to work for more extended periods.DIY projects can bring immense satisfaction, and a power feeder is a great addition to your workspace that can make a huge difference in workflow and safety. Building a power feeder also means you can customize to the specifications of your workspace and upgrade it anytime.
The world of CNC milling has experienced a remarkable transformation over the years, and today, individuals can access high-quality desktop milling machines at affordable prices. Desktop milling machines have opened up opportunities for hobbyists and small businesses by providing a cost-effective way to create precision parts out of a variety of materials. In this blog, we will explore different types of desktop milling machines, their benefits, and how they have revolutionized the manufacturing industry.One of the most affordable desktop milling machines is the DIY CNC Router Kits 2418 GRBL Control 3 Axis Carving Milling Engraving Machine, which retails at $239.99. It's an excellent entry-level option for DIY enthusiasts and beginners who want to create precision parts. The machine is easy to assemble and comes with a user-friendly control software.Alternatively, the STEPCRAFT-2/300 and STEPCRAFT-2/840 Desktop CNC Milling Machines made in Germany offer a more robust milling experience. These machines are designed to handle larger and more complex jobs. The STEPCRAFT-2/840 retails at $2,700.00, making it a bit pricier than the DIY CNC Router Kits 2418 but offers more advanced capabilities. It's worth mentioning that all StepCraft milling machines come with a 2-year warranty, making them an excellent investment for small businesses.For those who want to create 3D carvings, the USB CNC Router 4-axis 6040 1.5KW Spindle Engraving Milling 3D Carving machine is a great option. This machine offers superior precision when handling complex 3D designs and retails at $1,185.00. It comes with a USB interface for easy data transfer and compatibility with various software.The 3 Axis 3018 GRBL Control Mini CNC Router Milling Wood Engraving Machine Printer and the Mini 3 Axis 3018 CNC Laser Machine Carving Milling Router Engraver GRBL Control are other affordable options for those on a budget. They retail at $222.88 and $194.00, respectively, and are suitable for both hobbyists and professionals.If you're looking for a more advanced option, then the 4 AXIS ENGRAVER USB CNC6040Z ROUTER ENGRAVING DRILLING MILLING MACHINE 3D CUTTER is worth considering. It's designed for both industrial and personal use and retails at $1,097.90. The machine's 4-axis controller allows for complex jobs to be completed with ease.The DIY 2417 Mini Engraving Milling Machine Engraver CNC Router PCB Metal Desktop is also an excellent option for those on a tight budget. At $202.40, this desktop milling machine is affordable yet powerful. It's easy to assemble, allowing beginners to create precision parts with ease.Finally, the 4 Axis CNC 3040 Router Engraving Drilling Milling Woodworking Machine 3D Printer is an ideal choice for woodworking enthusiasts. Priced at $619.00, this machine is designed to work with a variety of materials, including wood, plastic, and metal.Desktop milling machines have revolutionized the manufacturing industry by providing an affordable and accessible way to create precision parts from a variety of materials. These machines have applications in various fields, such as education, engineering, prototyping, and small scale production. The future of desktop milling machines is bright, and as technology advances, we can expect to see even more advanced machines hitting the market.In conclusion, desktop milling machines offer a cost-effective way for hobbyists, DIY enthusiasts, and small businesses to create precision parts. Regardless of your budget or skill level, there's a desktop milling machine that's suitable for your needs. The machines covered in this blog offer a wide range of applications and features, making them an excellent investment for anyone looking to improve their prototyping or production capabilities. When looking to purchase a desktop milling machine, consider the features, capabilities, and price to ensure you select the right machine for your needs.
Powerful and Versatile Stand Grinder Machine: A Must-Have Addition to Your Workshop
release regarding the newly launched stand grinder machines.Introducing the Revolutionary Stand Grinder Machines for Precision GrindingIn a world where precision and accuracy is key to achieving success in every industry, the need for high-quality grinding machines cannot be overemphasized. Precision grinding is a vital requirement in diverse industries such as manufacturing, automobile, medical, aerospace, and many others.Grinder machines have been produced over the years to meet the needs of various industries. However, few can compare with the newly launched stand grinder machines. Our company has designed a unique and revolutionary grinder that promises to transform the production process of our customers.Our stand grinder machines standout features include robustness, durability, versatility, accuracy, and low maintenance cost.Robustness and DurabilityOur stand grinder machine is manufactured with high-quality materials, which makes it robust and durable. With this feature, the grinder machine can withstand harsh working conditions, including high-temperature and rough handling.VersatilityOur stand grinder machine’s versatility is another spectacular feature that will interest our customers. It is designed for both wet and dry grinding. This means that the machine can grind various types of materials and components in different forms.In addition, the stand grinder machine comes in different sizes allowing our customers to select the machine that meets their specific needs. Our engineering team's flexibility ensures that the grinder machine meets our customers' requirements with bespoke designs made to order.AccuracyWhen it comes to precision and accuracy, our stand grinder machine stands out. It is designed with advanced technology that allows for precise grinding to the slightest detail. The grinder machine enables accurate and consistent workpiece grinding with our unique programming software.Low Maintenance CostOur stand grinder machine is designed with such precision that it requires minimal maintenance cost. The machine does not require any specific skills to be maintained, meaning our customers can operate and maintain the machine with ease, which ultimately saves money in the long run.Our company acknowledges that the stand grinder machine’s outstanding features would not be achieved without our highly skilled professionals' dedication and commitment. We continually seek to improve our products' quality, ensure that our products meet international standards, and guarantee customer satisfaction.Our state-of-the-art manufacturing facility equipped with the latest technology enables us to produce high-quality machinery.Conclusively, our stand grinder machine's launch is a game-changer in the machine tools sector, and we believe that this machine's precision grinding is set to transform the manufacturing industry. We welcome inquiries from companies interested in owning our revolutionary stand grinder machines. Contact us today to order and enjoy a highly efficient, precise, and reliable machine that meets every need.